Definição de falha e como identificá-las em produtos no geral
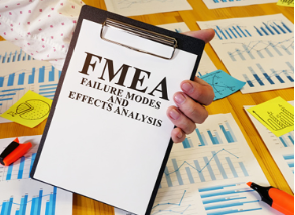
A análise de falhas é dada pela metodologia FMEA (Failure Mode and Effect Analysis), que significa Modo de Falha e Análise de Efeito. Essa metodologia busca encontrar possíveis problemas, suas causas raízes e suas soluções. Esses problemas podem ocorrer tanto em produtos, quanto em processos.
A FMEA de produto engloba as falhas ocorridas em produtos dentro de um projeto, como a projeção de um airbag de um novo automóvel. Já a FMEA de processo abrange as falhas que acontecem no planejamento de um processo, como por exemplo na fabricação de um cinto de segurança.
A FMEA pode ser realizada seguindo alguns passos: a definição do produto ou processo que será analisado, a escolha dos profissionais que trabalharão nessa análise, a análise das informações sobre o produto ou processo escolhido, a identificação dos efeitos que cada falha pode causar, a busca pelas causas raízes dessas falhas, a análise do RPN (Risk Priority Number), nível de risco de cada falha, a realização de ações preventivas para prevenir essas falhas, a elaboração de um documento que abranja tudo que foi feito no FMEA, e o acompanhamento do produto ou processo escolhido.
Passos para a realização da FMEA
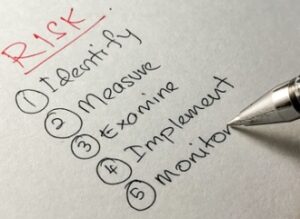
O grau de criticidade do processo ou produto escolhido. Esse grau pode ser alto, médio ou baixo. Quando o grau é alto, significa que o processo ou equipamento é muito importante, devendo ter uma análise de falhas sem erros. Também é necessário levar em conta a severidade, probabilidade e defectibilidade da falha.
Estrutura do Diagrama de Ishikawa
A busca pelas causas raízes dessas falhas pode ser feita por diversos métodos: 5 Porquês, no qual a resposta do primeiro porquê forma um novo questionamento, um novo porquê, para a próxima pergunta até que se atinjam 5 porquês; o Diagrama de Ishikawa, o qual tem o formato de uma espinha de peixe, no qual a espinha é o efeito e os desdobramentos são as causas, podendo ser essas de método, mão de obra, material, medida, meio ambiente e máquina, cuja estrutura está representada a seguir.
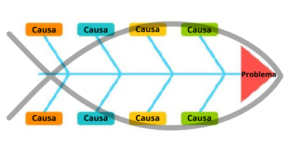
Continuando os métodos, pode-se utilizar também: Diagrama de Pareto, o qual apresenta graficamente as falhas e a frequência com que ocorrem; Diagnóstico IA, pela análise constante de equipamentos e processamento dos dados relacionados a eles; e Árvore Lógica das Falhas, na qual devem definir-se na sequência os evento, os modos de falhas, as causas físicas, e as causas humanas. Se quiser saber mais sobre esses cinco métodos apresentados, clique aqui.
Por que analisar as falhas?
A manutenção industrial está cada vez mais eficaz dentro das empresas, não só para consertar equipamentos quebrados ou que não estão com um bom desempenho, mas também para prever falhas, reduzir o custo de manutenção, aumentar a confiabilidade das máquinas e muito mais. Nesse sentido, a análise de falhas é um processo extremamente necessário, já que consiste em analisar a ocorrência dos problemas para encontrar a causa e a solução mais eficaz.
Sempre que a FMEA é colocada em prática, o resultado deve ser um plano de ações com detalhes precisos sobre o que deve ser feito. Visando desenvolver procedimentos específicos que estabeleçam se a melhor forma de tratar um determinado risco é com uma ação preventiva ou corretiva. Para isso, deve ser formulada uma hipótese que engloba uma sequência de eventos responsáveis — direta ou indiretamente — por aquela falha. Com base nessa investigação, medidas preventivas e corretivas serão feitas.
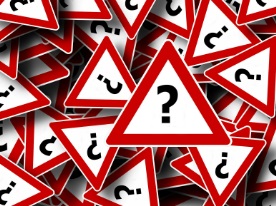
Além de necessário, a análise de falhas precisa ser livre de erros. Sua eficácia está atrelada ao funcionamento da indústria como um todo. Caso seja realizada de forma inadequada, os técnicos de manutenção não conseguem prever os erros, aumentando as chances de paradas inesperadas que prejudicam toda a produção e o risco de acidentes de trabalho.
Como realizar um tipo de analise de falhas?
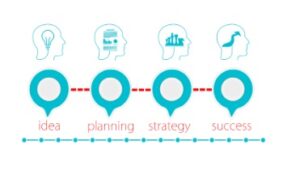
Para realizar uma análise de falhas eficaz, alguns passos podem ser seguidos, como:
- Identificar o problema.
- Verificar as possíveis causas: identificar as causas do problema, ou seja, se ele ocorreu por falha humana, falta de manutenção, por dano elétrico ou outras questões.
- Analisar se as possíveis causas, de fato, resultaram no problema.
- Analisar e controlar a falha: após a análise das causas, é preciso impedir que o problema continue afetando a indústria.
- Avaliar o problema: aqui é necessário analisar o problema como um todo. Para isso, é preciso saber o índice de ocorrência, a severidade, a detecção e o risco gerado.
- Desenvolver ações corretivas e de prevenção.
- Acompanhar o andamento das ações realizadas: Acompanhar o desenvolvimento da máquina ou processo para ter certeza de que o problema foi resolvido.
Visando que a FMEA pode diminuir a probabilidade de falhas em produtos e processos futuros, diminuir a possibilidade de falhas que não eram conhecidas antes de ocorrerem, aumentar a confiabilidade de produtos e processos a fim de desenvolver o negócio, e diminuir o risco de erros, é muito bem justificável as vantagens ao se adquirir o serviço de consultoria da Química Jr., que trata dentre outras coisas sobre a análise de falhas.
Se você ainda não está convencido, clicando aqui você descobre 6 motivos para contratar uma consultoria da Química Jr. e desenvolver uma FMEA que auxilie seu negócio em muitas vertentes.
Além disso, clicando aqui você conhece mais sobre o conhecimento especializado trazido pela consultoria e como ele pode desenvolver seu trabalho, ou então clicando aqui para descobrir de uma vez por todas a diferença entre consultoria e P&D, serviços que a Química Jr. busca desenvolver com excelência.